Coweta American | สล็อตเว็บตรง เว็บสล็อต ค่ายใหญ่ API ตรง อันดับ 1
สล็อตเว็บตรง Coweta American เว็บสล็อต API ตรง ค่ายใหญ่ ไม่ผ่านเอเย่นต์ ฝากถอนออโต้ ไม่มีขั้นต่ำ อันดับ 1 เล่นได้เลยที่ CowetaAmerican.com
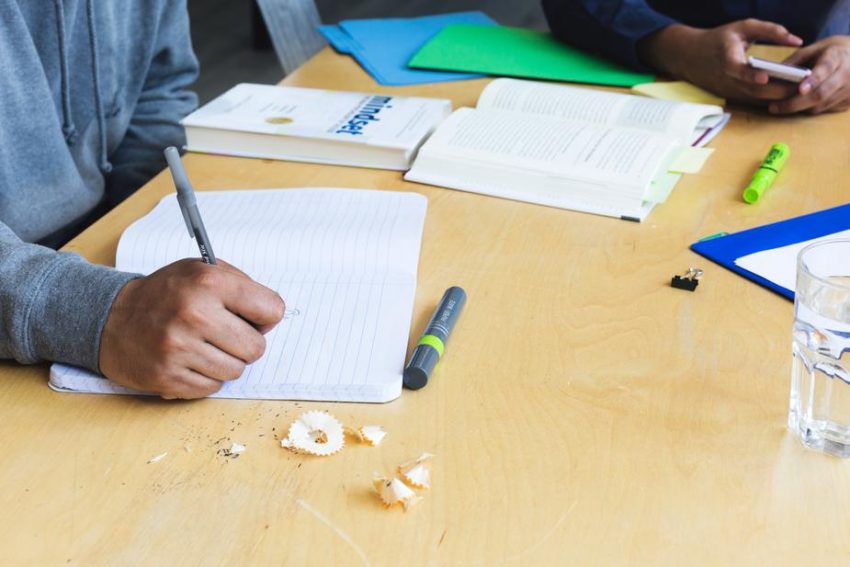
A bibliography writing tips
Posted on 05/05/2020
Whether or not you’re tackling formal essay writing or an undergraduate dissertation, many college students discover it daunting the primary time they’re required to jot down a bibliography on the finish of a chunk of labor. Concern not – not solely is it a lot simpler and scary than you would possibly suppose, however we…
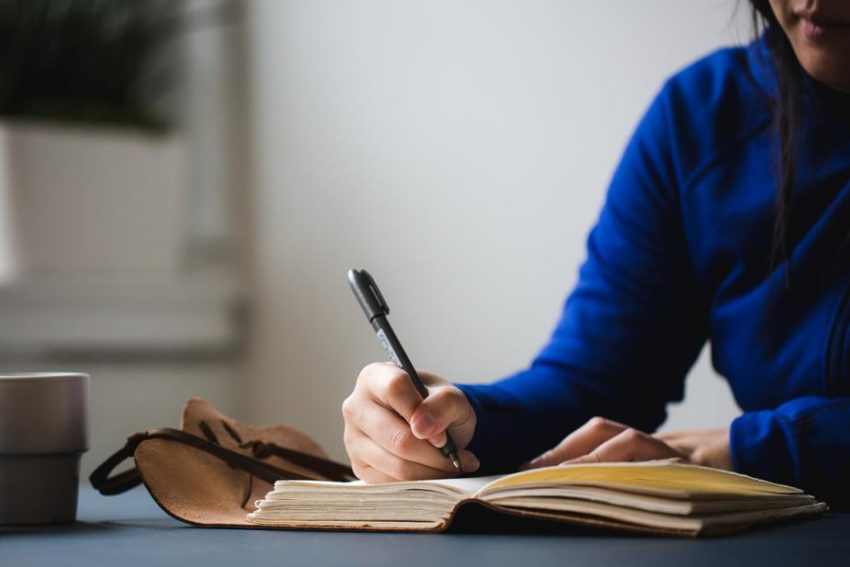
The best essay writing
Posted on 17/04/2020
A primary-class essay is one that’s categorised by a grade of 70 per cent or larger, although in some establishments the minimal requirement is 75 per cent. Regardless of the case, for a lot of college students this benchmark appears nearly inconceivable to achieve.Relaxation assured, nonetheless, that there are steps you could take to assist…
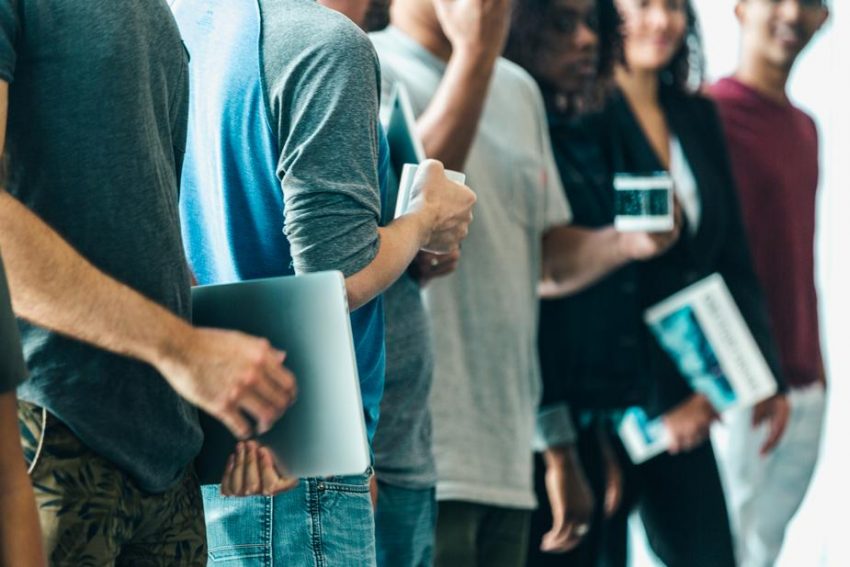
What is a Masters essay
Posted on 15/03/2020
When it comes to howto compose a Experts composition, it may be challenging to fully grasp and get the delicate differences amongst Experts and under graduate degree job. In a nutshell, a Masters degree essay will usually necessitate a deeper degree of different consideration, which is exhibited by embracing these thoroughly tested hints. Mastery Since…
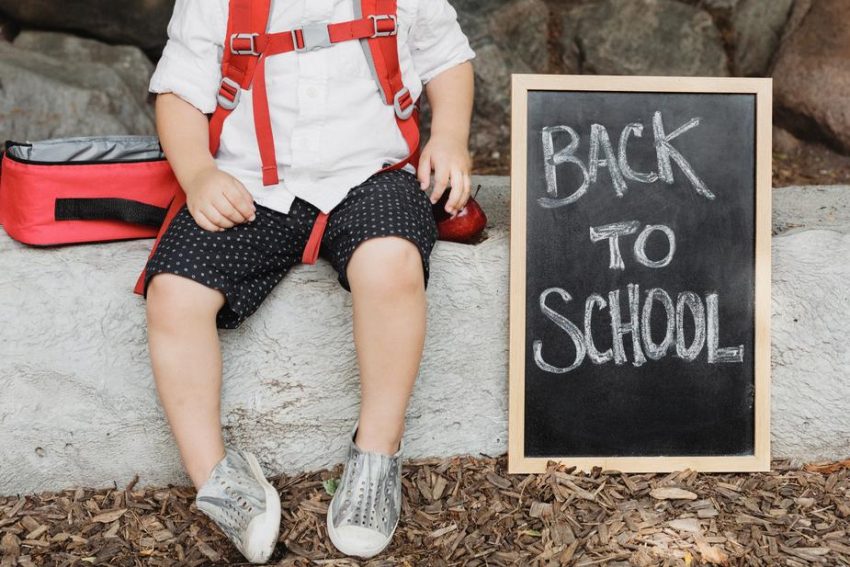
What you need to know about Peer Editing
Posted on 07/02/2020
Your professor simply assigned you one other scholar’s essay to look evaluation, however perhaps you don’t know the place to start out. That’s okay! Let’s begin by taking a number of the thriller out of the equation. A peer evaluation, additionally known as peer enhancing or a peer workshop, is while you learn one other…
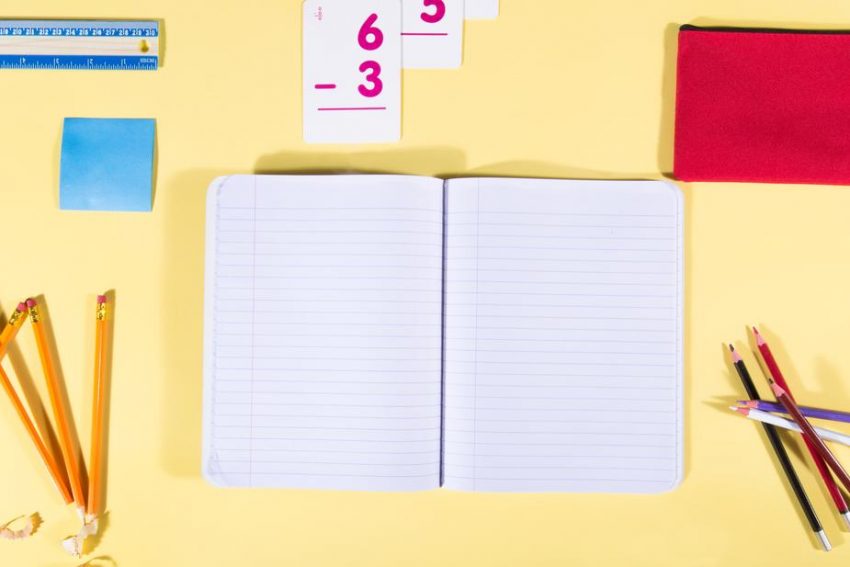
A DBQ Essay the Easy Way writing tips
Posted on 01/01/2020
What if I advised you that you just needed to write a analysis paper however that you just didn’t really must do any of the analysis? Fairly candy deal, proper? A document-based query (DBQ) essay is form of like that. You must write an essay utilizing a wide range of sources, however another person supplies…
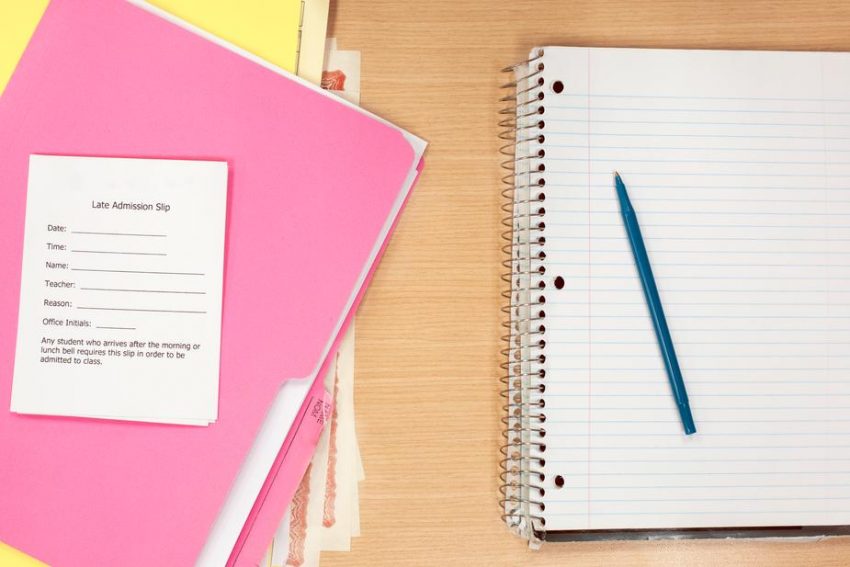
A Group Essay writing tips
Posted on 25/12/2019
A group essay project can really feel a bit like some form of morbid social experiment. A number of strangers are compelled to work collectively on a venture that’s typically acknowledged as being extra simply carried out alone. Will they discover a option to work collectively, or will they descend into chaos? With out the…
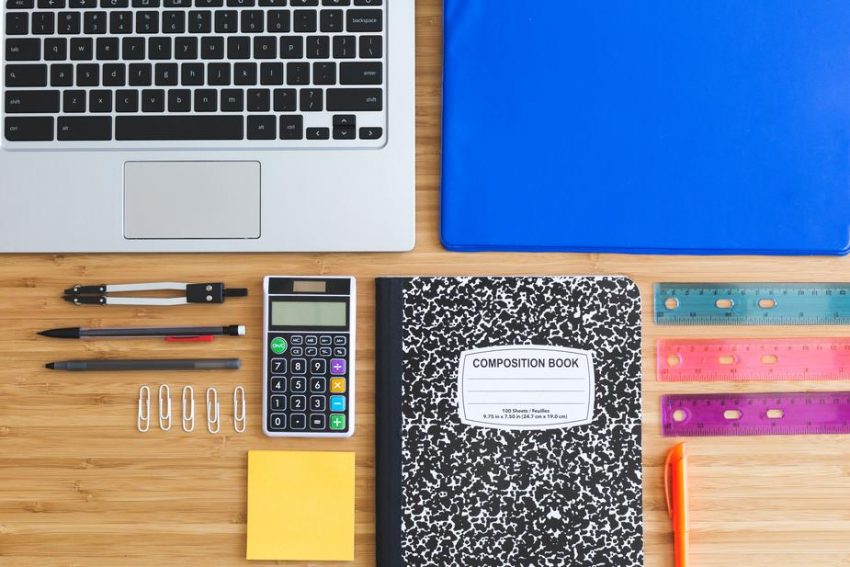
How to write a Policy Brief
Posted on 14/11/2019
It’s late at night time, and also you’re determined to discover a good film. You begin scrolling via the hundreds of choices supplied in your favourite video streaming service. What if as a substitute of a brief two-line abstract of every film, the service solely supplied a three-page detailed overview and evaluation? Who has the…
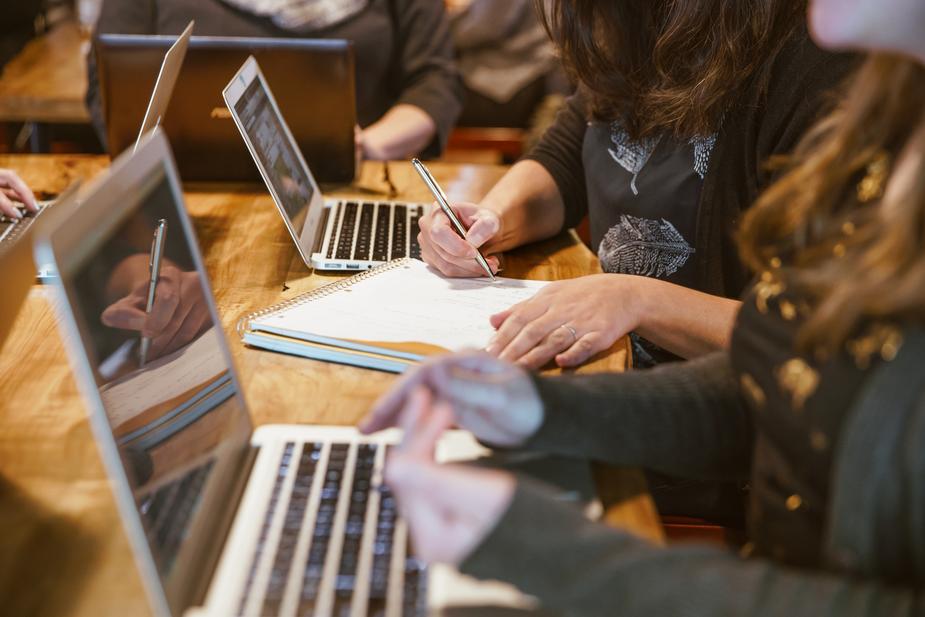
A Personal Statement writing tips
Posted on 13/10/2019
You’ve taken the required exams. You’ve stuffed out on-line and paper types. You’ve despatched in your highschool transcripts. You’ve possibly even requested some letters of advice to assist seal the deal. However as these admissions deadlines strategy, you continue to have one factor left–the dreaded private assertion. Certain, you’re only one hopeful pupil in an…
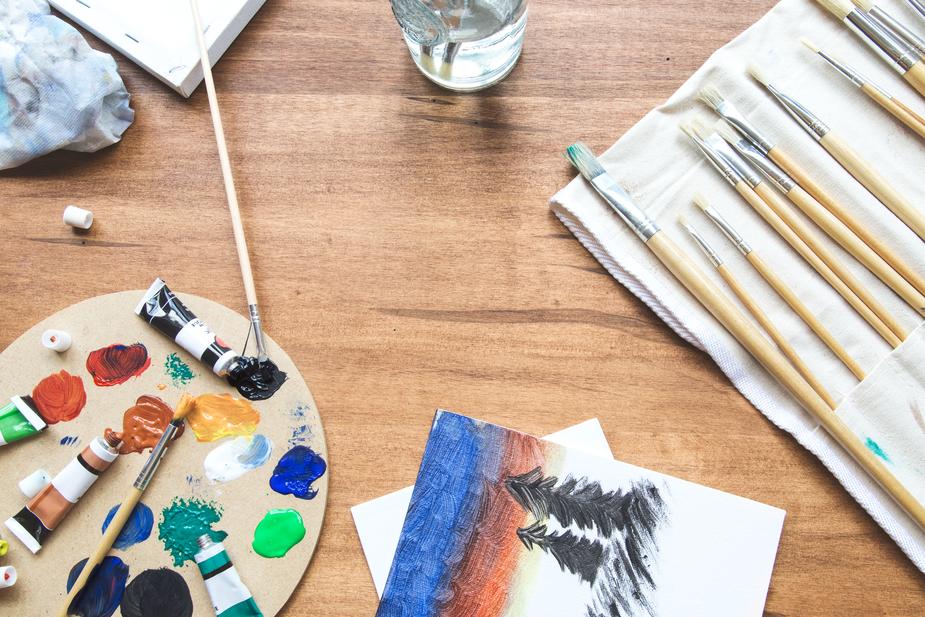
Writing Time Management
Posted on 06/10/2019
Have you ever ever wished you possibly can journey in time to complete all of the issues you must do? To repair one thing, to do higher on a take a look at or an essay, to unlock a while for a trip? Properly, guess what? You…you continue to can’t do this. Sorry. However you…
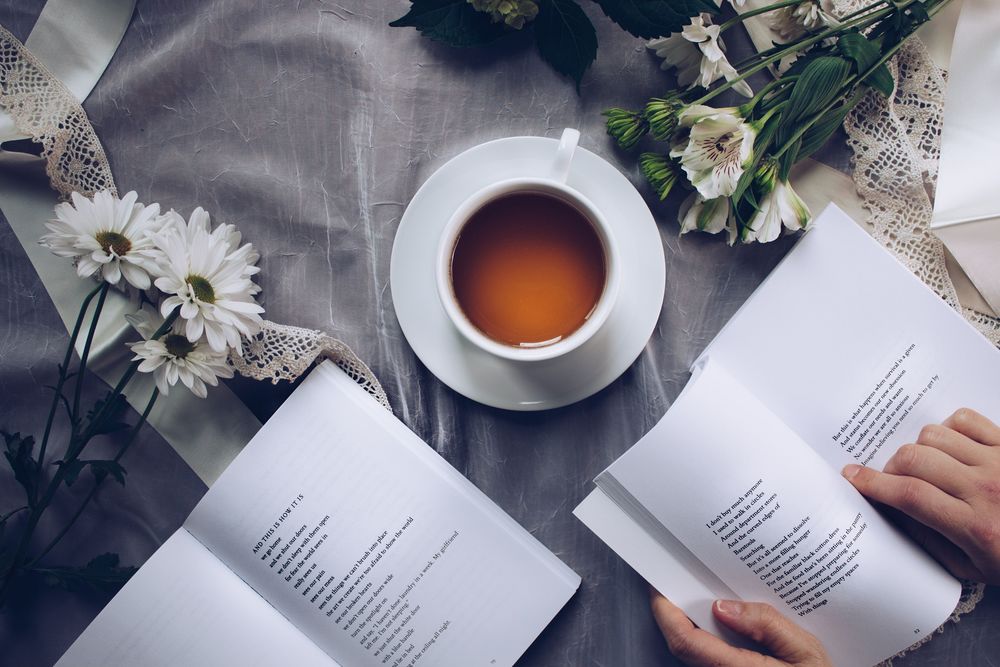
How agencies help to avoid expulsion
Posted on 02/10/2019
Sometimes you underestimate the work of agencies in writing dissertations and term papers. It seems to you that you just pay money, and the author does his work. However actually, have you ever wondered that writing agencies do a great job for students? In fact, it is not simple so many people address to such…